
Short brief of a design collaboration with Internorm
In the lines below I will introduce you to few key insights of our design collaboration, I will share with you certain details and our approach to design process.
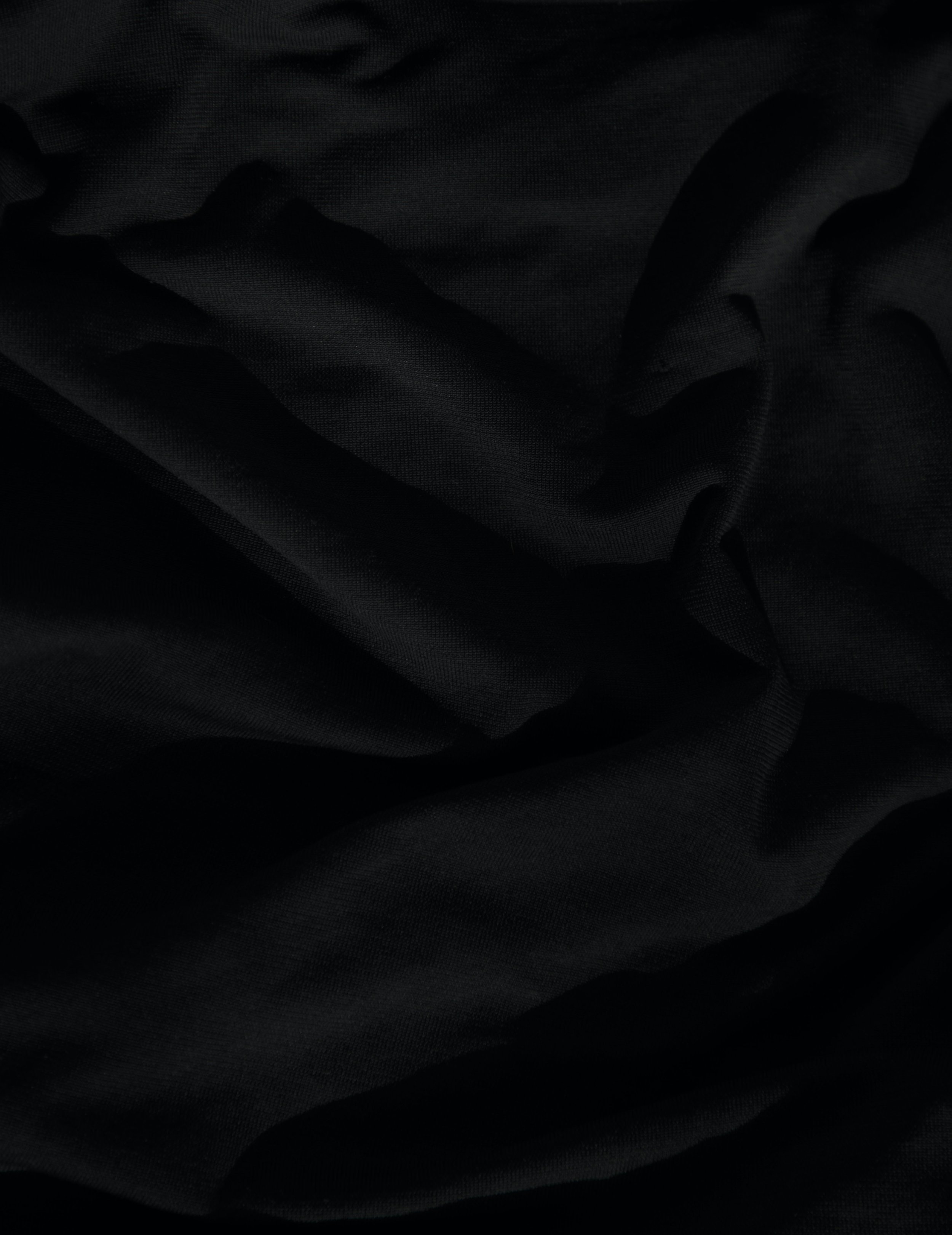
Envisioning new future.
Universe is a constantly evolving field of energy and everything in our known reality is evolving with it. Although nature is a self organising, self evolving system, we humans tend to create new future by imagining it.
Sometimes inspiration comes suddenly and from nowhere, sometimes it comes from necessity to solve a certain problem and other times it comes simply by imagining a brighter future we want to live in. And once the vision for the new future is present in our mind we can start to design it into life.
With the Internorm our goal was not just to create a few new door designs, but to make designs that will also positively impact our quality of live.
Our inspiration was to make the designs that will be more timeless, more inspiring and more friendly to interact with.
Putting vision into words is fairly easy thing to do, however to really feel the future and to imagine it to such a degree that you can execute on it and bring it to live is a process not everyone is familiar with.
And at this point I am inviting you to dive in a little deeper with me, and explore few secrets of our design process.
Are you ready?
OK…
As you have read above we have set few characteristics which we want our design to reflect and then we have substitute those with values such as … , …,
(You can read more about them at our “About design” page.)
Once the mission was set we started with our so called “discovering possibilities process”
Within this process we let our imagination to flow without any limits, we make unlimited amount of sketches and try to encapsulate the feeling off all wanted characteristics and values in one design. And the more sketches are done within this process the more we know what we want and need and in which direction we have to move further.
At one point, in our case we have stopped at our 174th sketch, where we believed we have generated enough ideas and concepts to fulfil our initial vision. At this point we have chosen the best sketches, the best designs and we went ahead with a new layer of development and we started to mould those designs into reality.
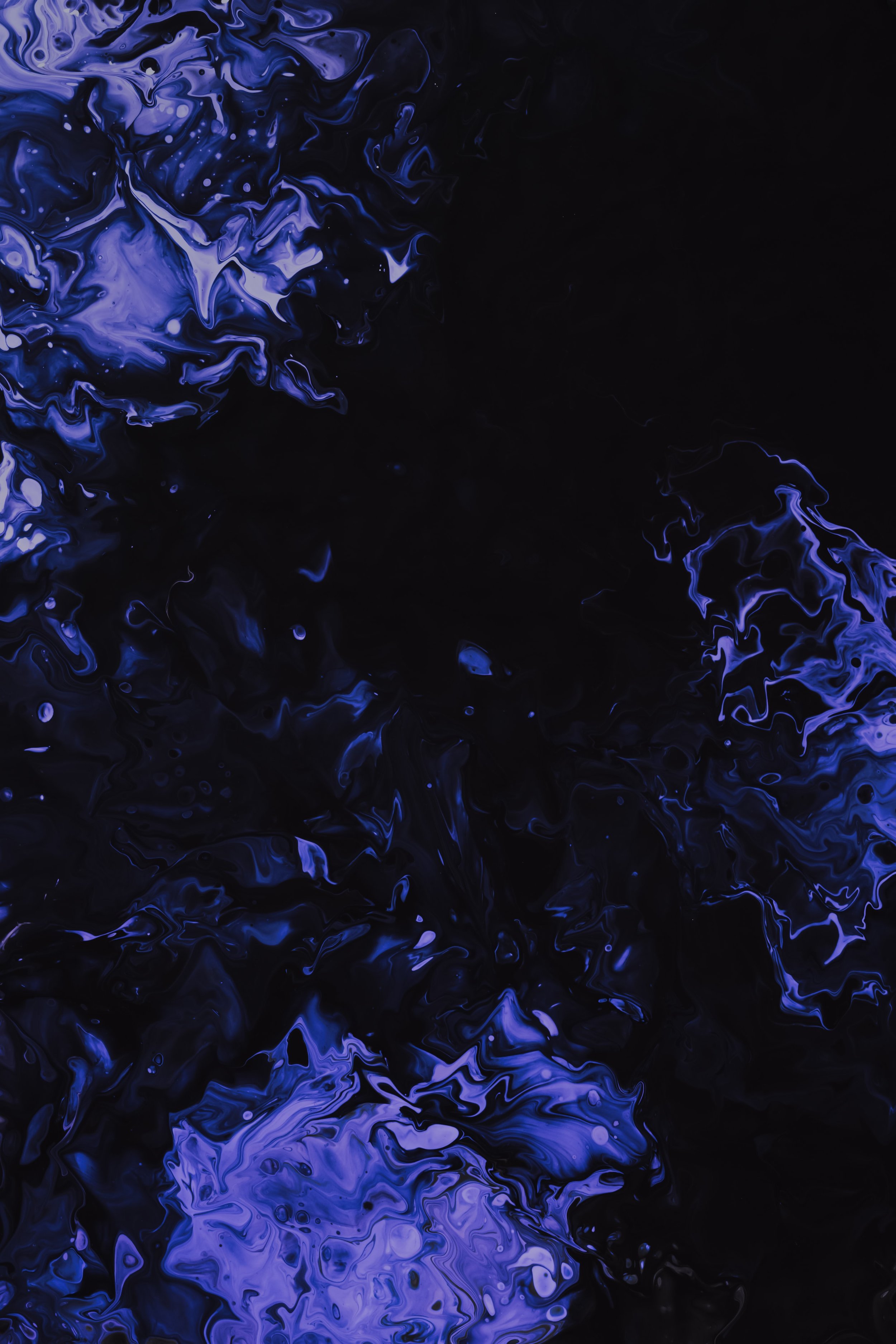
Moulding imagination into reality.
Here comes the time in the process where you actually start testing and predicting how the product could look like in real world. Although the imagination has no limits, there are certain rules in our three-dimensional reality, that you kind of have to take into consideration in order to give a life to a product.
Again not everyone has the skillset to move across this point of process, and those who do, they hold a responsibility to design a product that at the end is genuinely worth making and has a positive impact on the world.
Are you curious how we have navigated through this process?
Here you go…
For this process we took our sketches (174 of them if I am exact), our best ideas and start to moulding them within the rules of physics, usable dimensions, and requirements of mass production. By the end of the selection only 33 of 174 sketches were eligible to be translated into 3D CAD models.
Modelling involves crafting the lines from sketches into the shape of metal, glass and other materials, working endlessly to enrapture the emotions from the sketch, and simultaneously making the design aesthetically attractive and comfortable on touch and intuitive to use.
There is not much secrets to this process though, but it involves a lot of playing around, testing the aesthetics, different material combinations, trying out different handle sizes, different positions of the windows, different radiuses, panel widenesses, etc,…
The goal is to recreate the feeling from the initial sketches which were driven by sheer imagination. And to come as close to this point as possible you have to test a lot of different variations of shapes and proportions to really see what will work the best.
I have tried to write this to you in a bit more exciting way, yet the truth here is that within this process there is a lot of failed attempts for synchronising the designs and a lot of beautiful design sketch concepts that had to be left behind because they were only beautiful and exciting on a paper and were not scalable for requirements of the real world.
But if you take into account that this is only a part of the process which in the end leads to the creation of something beautiful, then it actually becomes exciting, because you know that it will lead you to creating something worth making.
As you can translate from the title of this paragraph the point of this process is to seamlessly transfer initial imagination, initial feeling and impression from your mind and later your sketch and to mould it in our three-dimensional world where it will serve a greater purpose.
From 33 of the chosen sketches there were only 15 of the designs which made it through all of the requirements into usable 3D CAD models. And those were the models which made it to the finals. Those designs were realistically rendered in computer and were presented to the Internorm where they took final inspections and choose a selection of the top 6 really great designs which fit their needs the best.
Once the final design selection were declared, it was time to really polish the designs and make them truly unforgettable.
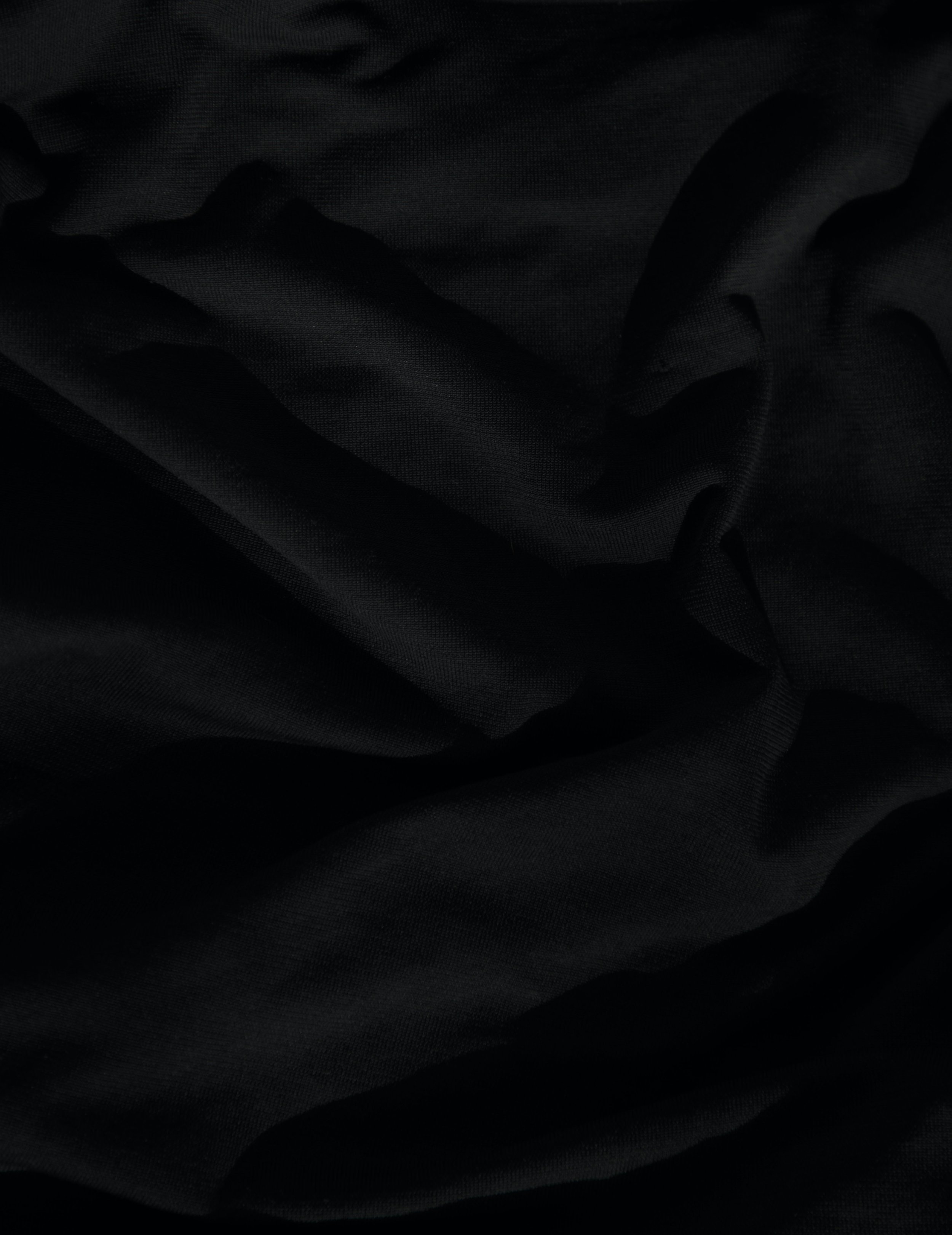
Making it unforgetable.
I dont know about you but for me this is my favourite part of the design, this is the process where the cream rises to the top, this is the part of the process that makes the difference between the leader and the follower, difference between great and legendary.
The more you invest your attention into the details the more refined the product become and the deeper to its soul you are able to see.
And to not to hide this insight from you, in the following lines I will let you know a bit more about this design stage.
You are probably curious how something can actually become unforgettable. Right?
Let's take a look…
At the moment when we have our design concept moulded into reality, at this point we have created about 90-95% of final version of the product, yet there is about 30-50% work left to be done.
It is the refinement of the product, the sheer details and final adjustment for production efficiency which creates really huge difference in how we perceive the product once it is being made.
And why is that?
We humans are really good at sensing the even slightest details and if you think about it more we actually have the ability to feel if something was made by care or not.
The only thing why the details at times gets so little credit is because people are just blindly stating that they are not so important since they have never put attention into understanding the mechanics of it, but if you put your focus on opinions on the biggest creators of our time they will tell a different story.
(more about the design you can read on “about design” page)
Ok, let me now show you some examples how we have tackled the refining of the Internorm new door designs.
One of the biggest things was refining the design proportions of the doors, perfecting the windows positions and sizes, declaring handle sizes and positions, adjusting the radiuses all across the surface to get just right amount of softness and sharpness out of the design. In addition to that we have supplement the designs with right color tonalities, surface finishes and customisable side panels. Getting all those things right, down to the last millimetre, making sure the design becomes as intuitive, as exciting and as timeless as possible is the core and art of this process.
Once the proportions were set we have moved to the next step, which was at the first glance just the opposite of refining the proportions, it was the process of creating the design rules to make the design scalable and that the design will remain looking great at all the different ratios and dimensions which are required for the different door sizes. The dimensions did vary up to 500mm in width and height, and just for perspective this was 80% different from the initial “perfect” proportions we have set. The challenge here too was for the design models to psychologically appear the same regardless its ratio and size.
It is a stormy process, but it is always worth it, yet only few of us does it. :)
This was my short brief of our design process of creation the Internorm new door design.
I have tried to keep is as understandable and short for you to read through, sure not everything was mentioned in here
since at the end it is still 6 months of work described in 15 minutes and we have to
keep some secrets as well to stay competitive and one of the leading design companies. :)
Thank you very much for your time and attention for reading this page al the way through, I hope you get some value out of it.